Ein neues Verfahren für die additive Fertigung mit Holz ermöglicht einen Holzanteil von bis zu 85 % und Festigkeiten, die denen von konventionell hergestellten Holzwerkstoffen entsprechen. Mit diesen Eigenschaften eignet sich die sogenannte Individual Layer Fabrication (ILF) für eine breite Palette von Anwendungen in Design, Architektur und Technik.
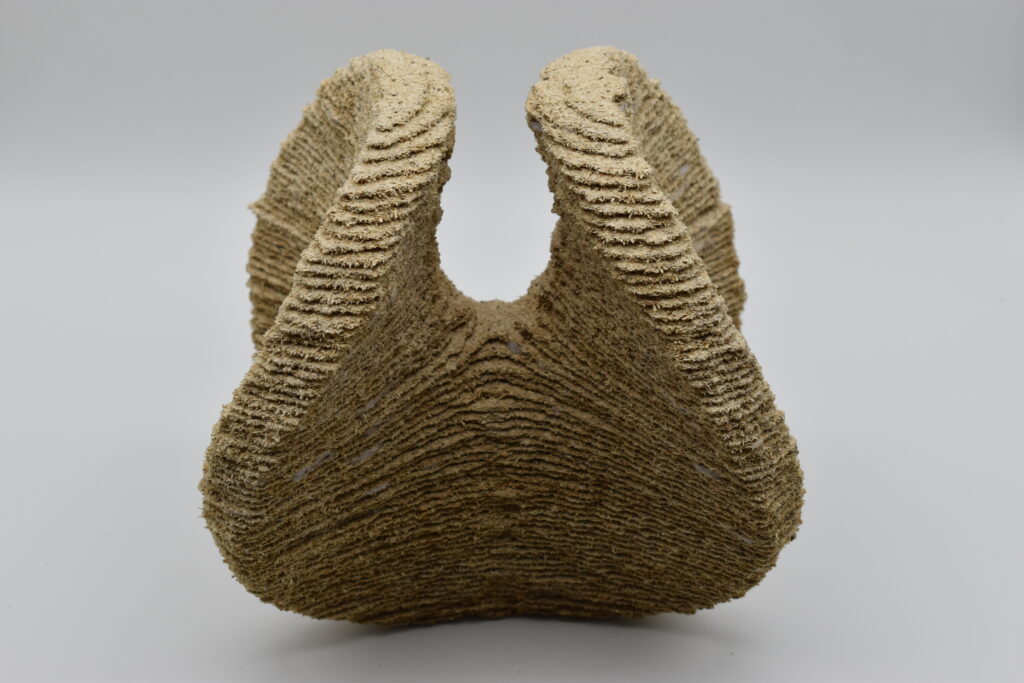
In der holzverarbeitenden Industrie fallen große Mengen an Restholz an, z.B. in Form von Sägemehl, Holzspänen oder Hackschnitzeln. Die additive Fertigung bietet die Chance, diese Abfälle in individualisierte, hochwertige Güter zu verwandeln. Neben den ökologischen Aspekten, die für die Verwendung eines solchen Rohstoffs sprechen, kann der Einsatz von Holz als Ausgangsmaterial in der additiven Fertigung dazu beitragen, die Materialeigenschaften zu verbessern und die Materialkosten zu senken.
Dementsprechend hat die additive Fertigung unter Verwendung von Holz in den letzten Jahren eine große Aufmerksamkeit erlangt. Filamente für Fused Filament Fabrication (FFF), die bis zu 40 % Holzpartikel enthalten, werden bereits von zahlreichen Herstellern auf dem Markt angeboten. Auch Binder Jetting mit Holzpartikeln ist möglich und wurde von Forust in einem Verfahren kommerzialisiert, bei dem die 3D-gedruckten Teile ihre endgültigen Eigenschaften durch eine Nachbehandlung mit Epoxidharz erhalten.
Die Kernidee von ILF: mechanisches Pressen, integriert in einen additiven Fertigungsprozess
Mit dem Ziel, den Holzanteil in additiv gefertigten Holzwerkstoffbauteilen drastisch zu erhöhen, haben sich Forscher der Technischen Universität München (TUM) und des Fraunhofer-Instituts für Holzforschung (WKI) zusammengetan und ein speziell auf dieses Ziel zugeschnittenes Verfahren entwickelt. Bei diesem neuartigen Herstellungsverfahren, der so genannten ‚Individual Layer Fabrication (ILF)‘, werden Bauteile durch das Laminieren von aufeinanderfolgenden Schichten individuell konturierter Platten aufgebaut. Letztere werden dabei additiv, durch selektives Binden von Holzpartikeln gefertigt. Da jede Schicht einzeln hergestellt wird, kann bei der Produktion dieser maßgeschneiderten Holzwerkstoffplatten ein mechanischer Pressvorgang eingebettet werden. Dieser Einsatz von mechanischem Pressdruck, integriert in einen additiven Fertigungsprozess, ist die Kernidee von ILF. Sie führt zu einer deutlichen Erhöhung des Holzanteils wie auch der Festigkeit der so hergestellten Bauteile.
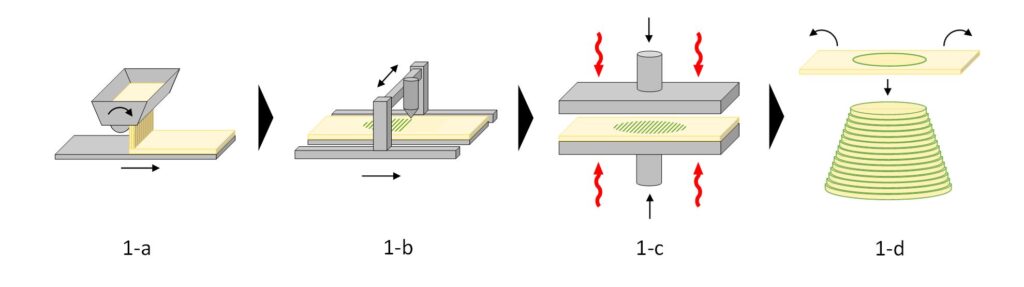
Die Funktionsweise des Holz-3D-Druckers: der ILF-Prozess im Detail
Praktisch lässt sich das ILF-Verfahren als eine Kombination aus Binder Jetting (bei dem Bauteile durch selektives Binden von Partikeln 3D-gedruckt werden) und Sheet Lamination (bei der Objekte durch das Laminieren von individuell konturierten Platten aufgebaut werden) beschreiben, ergänzt durch einen in die Prozesskette integrierten Arbeitsschritt des mechanischen Pressens. Grundsätzlich besteht die Individual Layer Fabrication demnach aus folgenden Arbeitsschritten: a) Holzpartikel werden in einer dünnen Schicht auf eine Arbeitsplattform gestreut. b) Auf diese Schicht wird Klebstoff aufgetragen, und zwar lokal begrenzt auf die Bereiche, in denen die Holzpartikel entsprechend der Zielgeometrie des Objekts gebunden werden sollen. c) Die so entstandene Hybridschicht wird unter Wärmeeinwirkung gepresst, wodurch der Klebstoff aushärtet. d) Schließlich wird das ungebundene Material entfernt und die individuell konturierte Platte aus gebundenen Holzpartikeln auf den Stapel der zuvor hergestellten Platten laminiert. Diese Grundversion des Verfahrens kann modifiziert werden, um die Effektivität des Prozesses zu erhöhen oder die Ergebnisse im Hinblick auf bestimmte Anwendungen zu optimieren: Die Reihenfolge der Arbeitsschritte kann z.B. geändert werden oder einzelne Schrittfolgen können wiederholt werden, bevor zum nächsten Arbeitsschritt weitergegangen wird.
Holzprodukte aus dem ILF 3D-Drucker: hohe Festigkeiten und geometrische Freiheit
Die mit dem ILF-Verfahren hergestellten Bauteile weisen Holzanteile von bis zu 85 Masseprozent und Biegefestigkeiten von bis zu 50 MPa auf; die Rohdichten liegen im Bereich zwischen 550 und 950 g/cm³. Mit diesen Eigenschaften erfüllen sie, oder übertreffen gar, die Anforderungen an konventionell gefertigte Holzspanplatten. Gleichzeitig ermöglicht das ILF-Verfahren ein hohes Maß an geometrischer Freiheit. Auf diese Weise können individualisierte, hochkomplexe Holzwerkstoffbauteile für eine Vielzahl von Anwendungen hergestellt werden. Zu letzteren gehören z.B. tragende und nichttragende Bauwerkselemente, Möbel, Vorrichtungen in der industriellen Fertigung oder Verpackungen. In diesem Video ist die Herstellung eines strukturoptimierten Holzdeckenelements durch 3D-Druck mittels Individual Layer Fabrication dokumentiert.
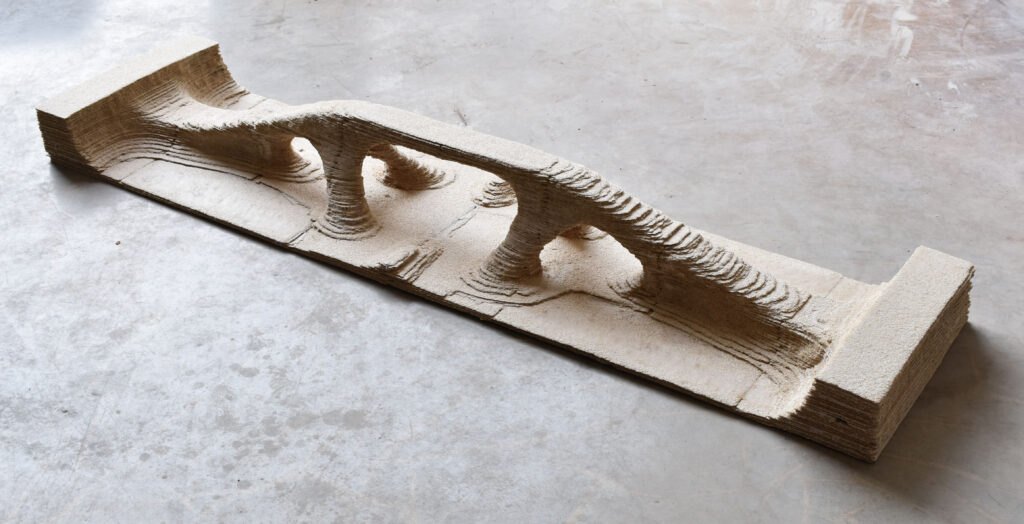