Additive Manufacturing macht mehr als nur Schlagzeilen. Die industrielle Revolution des 3D-Metalldrucks setzt Zeichen der Veränderung von Fertigungsstrategien. Und es werden Fakten geschaffen, die einen prinzipiellen Paradigmenwechsel für die Fertigung von Metallteilen ankündigen. AM setzt in der Substitution oder als hybride Strategie mit konventionellen Methoden der Zerspanung Akzente.
Einmal mehr zeigt sich die Luft- und Raumfahrt als Innovationstreiber und Speerspitze der digitalen Fertigung. Das jüngste Signal kommt von Thales Alenia Space. In Zusammenarbeit mit dem 3D-Druck-Dienstleistungsunternehmen Poly-Shape entstanden generativ gefertigte Teile für die neuen südkoreanischen Kommunikationssatelliten Koreasat-5A und Koreasat-7. Koreasat-7 soll 2017 in den Orbit auf Position 116º Ost gebracht werden, um von dort aus Südkorea, die Philippinen, Indonesien und Indien abzudecken. Koreasat-5A wird von der Position 113° Ost Korea, Japan, Indochina und den Mittleren Osten abdecken. Koreasat-5A soll noch vor dem zweiten Quartal 2017 auf Position gebracht werden.
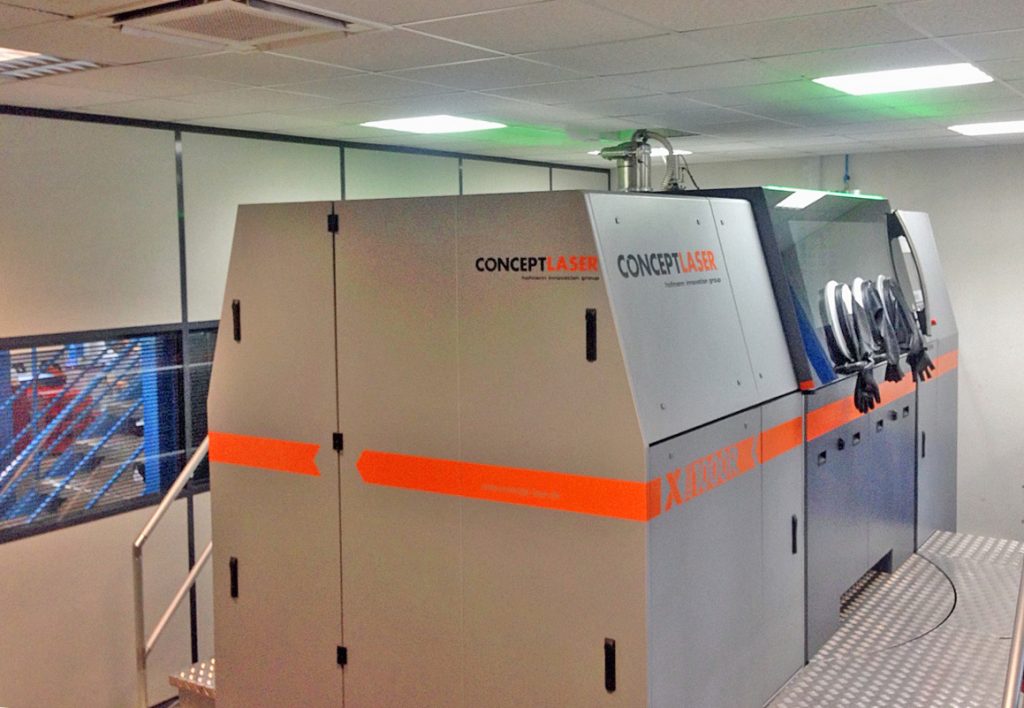
XXL-Bauteil entsteht in gemeinschaftlicher Zusammenarbeit
Die Antennenträger Koreasat-5A und Koreasat-7 werden die bislang größten Volumenteile des pulverbettbasierten Laserschmelzens von Metallen aus Europa im Orbit sein. Mit Abmessungen von 447 x 204,5 x 391 mm3 – und das bei einem Gewicht von nur 1,13 kg – kann man wirklich von einem Leichtbauteil sprechen. Eine Ingenieursleistung im XXL-Format. Die generativ gefertigten 3D-Bauteile dienen als Basisträger der Antennen der Satelliten Koreasat-5A und Koreasat-7, welche zur Kommunikation mit der Bodenbasis eingesetzt werden. In beiden Satelliten wurde ein identisches Teil verbaut. Die Abmessungen waren dabei eine echte Herausforderung für Thales Alenia Space. Sie wurden von der französischen Poly-Shape SAS hergestellt. Diese ist ein renommierter Partner der Luft- und Raumfahrtindustrie, wenn es um Prototyping, 3D-Metalldruck und Montagen geht.
Leichtbau und Kostenreduzierung als entscheidende Vorteile
Aluminium (Al) ist aufgrund von Gewicht und thermischer Leitfähigkeit das häufigste metallische Material für Satelliten. Je weniger Gewicht in den Orbit gebracht werden muss, desto besser. Florence Montredon, Leiterin AM bei Thales Alenia Space: „Die tatsächlichen Kosten, um ein 1 kg in den Orbit zu bringen, liegen als Daumenwert bei rund 20.000 EUR. Da zählt jedes Gramm. Das Startgewicht der beiden neuen Satelliten liegt bei rund 3.500 kg.“ Das Leichtbaupotenzial von AM war daher ein wichtiger Aspekt, um herkömmliche Fertigungsverfahren abzulösen. Für diese AM-Teile wählte Thales Alenia Space eine AISi7Mg-Legierung. Für Weltraumanwendungen werden hohe Festigkeit, Steifigkeit und Korrosionsbeständigkeit der eingesetzten Materialien gefordert. Im Zuge der Bauteilvalidierung zeigte sich zudem eine geringe Porositätsrate von
Maschinen- und Anlagentechnik von Concept Laser in XXL
Poly-Shape verfügt über 28 3D-Metalldruckanlagen, die verschiedene Bauraumgrößen aufweisen. Die größte Bauraumdimension für das 3D-Drucken mit Aluminium ist bei Poly-Shape derzeit eine X line 1000R von Concept Laser. Sie bietet einen Bauraum von 630 x 400 x 500 mm3 und verfügt über ein geschlossenes System für sichere Prozess- und Pulverführung entsprechend den ATEX-Richtlinien. Darüber hinaus verfügt die X line 1000R über einen Drehmechanismus zum wechselseitigen Einsatz von zwei Baumodulen, sodass eine permanente Produktion ohne Fehlzeiten garantiert ist. Diese einmalige Anlagenkonzeption führt nicht nur zu einer höheren zeitlichen Verfügbarkeit, sondern auch zu einem einfachen und vor allem sicheren Handling beim Rüsten und Abrüsten der Maschine. Das Nachfolgemodell, die X line 2000R, verfügt sogar über einen noch größeren Bauraum (800 x 400 x 500 mm3), welcher momentan weltweit einzigartig in Bezug auf das pulverbettbasierte Laserschmelzen ist. Das nutzbare Bauvolumen erhöht sich, gegenüber einer X line 1000R, nochmals um knapp 27 % von 126 l auf 160 l. Das Nachfolgemodell arbeitet zudem mit zwei Lasern mit je 1.000 Watt Leistung. Die Verfahrenstechnik des LaserCUSING von Concept Laser war für das Projekt von großer Bedeutung: Die Besonderheit der Anlagen von Concept Laser ist eine stochastische Ansteuerung der Slice-Segmente (auch „Islands“ genannt), die sukzessive abgearbeitet werden. Das patentierte Verfahren sorgt für eine signifikante Reduzierung von Spannungen bei der Herstellung von sehr großen Bauteilen. Bei enormen Abmessungen von 447 x 204,5 x 391 mm³ liegt es auf der Hand, den Verzug maximal beherrschen zu wollen. Die X line 1000R bietet eine ausbalancierte Temperierung des Bauraumes, um einen Verzug in den „übergroßen“ Bauteilen zu vermeiden. Natürlich ist die große, bionische und filigrane Geometrie im Aufbau zeitaufwendig: Es dauerte dennoch nur wenige Tage, um sie zu drucken.
Verfahrensgerechtes Konstruieren und Optimieren
Der Übergang auf AM bedeutet auch ein Umdenken in der Konstruktion. Um die Potenziale des Laserschmelzens vollständig auszuschöpfen, macht es keinen Sinn, eine Geometrie 1:1 nachzubauen. Leichtbau und Bionik erfordern ein verfahrensgerechtes Konstruieren.
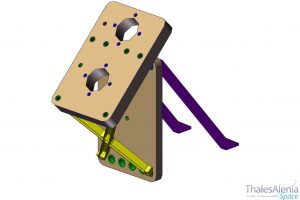
Dazu werden CAE/CAD-gestützte Methoden angewandt, um die 3D-Bauteile auf leistungsgerechte Geometrie, Bionik und Leichtbau zu trimmen. Das Design wurde in mehreren Durchläufen bei Thales Alenia Space optimiert (AM design optimization), beispielsweise auf die verschiedenen Techniken des Fügens und Montierens. Zudem wurde es in die Umgebung des Satelliten feinjustiert, um eine maximale Passgenauigkeit zu gewährleisten. In 2 – 3 Durchläufen wurde die Topologie optimiert. Anschließend wurden die CAD-Daten einem Redesign und Glättungen unterzogen, bevor eine mechanische Analyse und Simulation stattfand. Weiterhin wurde das Design auf die verfahrensbedingten Gegebenheiten im Bauraum mit Poly-Shape optimiert. Dies betraf die Orientierung des Teils im Bauraum und die notwendigen Supportstrukturen. Thales Alenia Space bezog auch Methoden des LBM ein (Layer Based Manufacturing). Florence Montredon: „Es ist klar, dass wir AM als guten Kandidaten für weitere Projekte identifiziert haben. In Zukunft möchten wir auch thermische Kontroll- oder Radio-Funktionen direkt auf oder innerhalb der 3D-Strukturen aufnehmen. Also Funktionsintegration als nächste Aufgabe. Auch dies ist eine logische Konsequenz aus den Potenzialen von AM.“
Fazit
Im Projekt Koreasat-5A und 7 wurde die Machbarkeit von hoch anspruchsvollen und sehr großen AM-Teilen für Anwendungen im Weltraum aufgezeigt. Das Redesign als generatives, bionisches Bauteil erlaubte es, die Teileanzahl von 9 Teilen auf ein Teil zu reduzieren. Der Herstellungsprozess konnte dank des Verfahrens in einem Schuss, also ohne den bisherigen Montageaufwand, gefertigt werden. Es ergab sich auch ein deutlich verbessertes Leichtbaupotenzial. 22 % der Masse konnten mit dieser AM-Lösung eingespart werden. Dies führte zu einem Endgewicht von nur 1,13 kg. Das war ein gewaltiger Sprung, wo es doch auf jedes Gramm bei diesen Anwendungen ankommt. Die 3D-Geometrie konnte optimal auf den Einsatz im Orbit hin getrimmt werden. Das Projekt zeigte anhand beeindruckender Ergebnisse die Potenziale der additiven Fertigung in der Raumfahrt auf und wird zukünftig sicher nicht das letzte dieser Art sein.
Interview mit Thales Alenia Space und Poly-Shape zum Projekt Koreasat-5A und Koreasat-7
Welche Techniken und Fertigungsmethoden wenden Sie zur Herstellung Ihrer Produkte an?
Florence Montredon: Aufgrund der sehr geringen Menge einzelner Bauteile für Satelliten und der geringen Menge an Satelliten generell, bietet sich der 3D-Druck ideal als Fertigungsoption an. Gussteile, also formgebundene Verfahren, bieten sich dem gegenüber eher bei Bauteilen an, die in größeren Serien gefertigt werden müssen.
Skizzieren Sie bitte kurz das Projekt Koreasat-5A und 7.
Florence Montredon: Mit der Herstellung der Telekom-Satelliten Koreasat-5A und Koreasat-7 wollten wir nachweisen, dass die Laserschmelztechnologie für unsere Anwendungen zahlreiche Möglichkeiten eröffnet. Die wesentlichen Vorzüge liegen in der kurzen Zeitachse von Konstruktion und Entwicklung bis zum fertigen Teil. Zudem in der hohen Wirtschaftlichkeit. Im Vorfeld unseres Projektes wurde zunächst ein erstes AM-Teil aus Aluminium gefertigt. Dieses Teil wurde erfolgreich im Jahr 2014 qualifiziert und für den Turkmenalem Monacosat im April 2015 eingesetzt. Die beiden neuen Teile für den Satelliten dienen als Basisträger der Antennen, welche zur Kommunikation mit der Bodenbasis eingesetzt werden. Sie sind ebenfalls aus Aluminium. Sie wurden von der französischen Poly-Shape hergestellt. Die erste Herausforderung war, dass wir zwei identische Teile brauchten: Sie sind Zwillinge – einen für Koreasat-5A und den anderen Zwilling für Koreasat-7. Die zentrale Herausforderung aber war die Größe. Im Vergleich zu unseren bisherigen Referenzen und Erfahrungen waren die Dimensionen der Teile enorm groß.
Bitte beschreiben Sie uns kurz die Teile.
Florence Montredon: Aluminium ist das häufigste metallische Material für Satelliten –aufgrund von Gewicht und thermischer Leitfähigkeit. Für diese AM-Teile wählten wir eine AISi7Mg-Legierung. Dieses Standardmaterial wurde bereits in der Gusstechnologie für Weltraumanwendungen validiert. Das Redesign als generatives, bionisches Bauteil erlaubte es uns, die Teile von 9 auf 1 Teil zu reduzieren. In einem Schuss, also ohne den bisherigen Montageaufwand. Es ergab sich auch ein deutlich verbessertes Leichtbaupotenzial. Wir sparten 22 % der Masse ein, was zu einem Endgewicht von nur 1,13 kg führte. Das war ein gewaltiger Sprung, wo es doch auf jedes Gramm bei unseren Anwendungen ankommt.
Stéphane Abed: Die Abmessungen sind 447 x 204,5 x 391 mm³. Eine enorme Dimension. Es dauerte etwa 6 Tage, um sie zu drucken. Es ist das bislang größte AM-Teil Europas für den Orbit.
Was waren die besonderen Herausforderungen, um das größte 3D-Metallbauteil zu bauen?
Stéphane Abed: Die Fragestellungen waren also z. B. Machbarkeit, Verzugsneigung, Geometrie oder auch Gewicht. Mit CAE/CAD-Werkzeugen zur Optimierung gelang es den Konstrukteuren, das Design, also die Geometrie, verfahrensgerecht zu optimieren und gleichzeitig Gewicht einzusparen und die Belastungsanforderungen zu erfüllen. Die Konstrukteure haben einen sehr guten Job gemacht. Das finale Design wurde dann in enger Zusammenarbeit und Interaktion von Thales Alenia Space und Poly-Shape für die Fertigung in zahlreichen Stufen des Redesigns optimiert und feinjustiert. Wir sprechen von einer bionisch optimierten Konstruktion.
Florence Montredon: Der Antennenträger wurde dann spezifischen Bodentests unterzogen. Dazu zählen Vibrationstest und hohe Temperaturen im Vakuum, um eine geforderte Lebensdauer von 15 Jahren im Orbit zu testen.
Wie kamen Sie zum Laserschmelzen?
Florence Montredon: Laserschmelzen ist ein sehr vielversprechendes Verfahren für Satelliten-Anwendungen. Es passt perfekt zu geringen Stückzahlen, eröffnet Spielräume für den Leichtbau und eignet sich ideal für sehr komplexe Geometrien.
Welche Erfahrungen haben Sie im Projekt mit dem Laserschmelzen im Vergleich zu den bisherigen Fertigungsstrategien gemacht?
Florence Montredon: Die pulverbettbasierte Laserschmelztechnologie eignet sich zur Optimierung des Designs und ermöglicht eine signifikante Einsparung an Gewicht. Und Gewichtsreduktion ist für uns eine der wichtigsten Zielvorgaben. Die tatsächlichen Kosten, um ein 1 kg in den Orbit zu bringen, liegen als Daumenwert bei rund 20.000 EUR. Das Weltraumrecht ermutigt uns, auch die Menge an metallischen Werkstoffen in Flugobjekten zu verringern, weil sie eine Gefahr von Emissionen beim atmosphärischen Wiedereintritt des Satelliten darstellen. Es geht also um Leichtbau, Nachhaltigkeit und einen Beitrag zum Umweltschutz. Natürlich erwarten wir von diesen Technologien auch Kostenreduzierungen und Vorteile im knappen Zeitplan von Weltraummissionen. Wir haben im Projekt ein Kosteneinsparungspotenzial von rund 30 % gegenüber der bisherigen konventionellen Lösung mit Montage ermittelt.
Wie kam es zur Zusammenarbeit von Thales Alenia Space und Poly-Shape?
Florence Montredon: Wir trafen das Team von Poly-Shape im Jahr 2010 anlässlich eines französischen F&E-Gemeinschaftsprojekts. Uns wurde dabei schnell klar, dass das Team von Poly-Shape ein strategischer Partner für unsere AM-Entwicklungen wird. Wir entwickelten sehr erfolgreich und vor allem schnell die ersten Aluminiumteile zusammen. So war es natürlich ideal für diese neue Herausforderung, um wieder mit ihnen zusammenzuarbeiten.
Warum fiel die Wahl auf Anlagen von Concept Laser?
Stéphane Abed: Concept Laser bot sich hier besonders an, weil diese Maschinen die einzigen sind, die für den 3D-Metalldruck die nötigen Bauräume anbieten. Es gibt derzeit keine Alternativen, außer man nutzt kleinere Bauräume und fügt die Teile in der Fügetechnik zusammen. Dies bedeutet das Risiko von Schwachstellen. Die theoretische Alternative wäre es gewesen, die Teile in zwei Hälften zu drucken und zu fügen, aber wir hätten den Vorteil der hier möglichen Montagereduzierung aufgegeben. Zudem hätten sich beim Fügen möglicherweise Defekte gezeigt, die mit der One-Shot-Option des Laserschmelzens auszuschließen sind. Nicht zu vergessen – in einem Teil sind wir schneller am Ziel.
Welche Anlagen setzten Sie bei Poly-Shape für den 3D-Metalldruck ein?
Stéphane Abed: Poly-Shape verfügt über 28 3D-Metalldruckanlagen, die verschiedene Bauraumgrößen aufweisen. So können wir bei den Dimensionen auf die meisten Kundenwünsche eingehen. Prinzipiell sind wir auf Rapid Prototyping und Kleinserien ausgerichtet. Die größte Bauraumdimension für das 3D-Drucken mit Aluminium ist bei Poly-Shape derzeit eine X line 1000R von Concept Laser. Die Technologie heißt LaserCUSING. Die Verfahrenstechnik des LaserCUSING war von hoher Bedeutung: Die Besonderheit der Anlagen von Concept Laser ist eine stochastische Ansteuerung der Slice-Segmente (auch „Islands“ genannt), die sukzessive abgearbeitet werden. Das patentierte Verfahren sorgt für eine signifikante Reduzierung von Spannungen bei der Herstellung von sehr großen Bauteilen, wie in diesem Fall. Die X line 1000R bietet eine ausbalancierte Temperierung des Bauraumes, um einen Verzug in den „übergroßen“ Bauteilen zu vermeiden. Zudem können wir auf dieser Anlage nicht nur Aluminiumteile, wie bei Satelliten üblich, aufbauen, sondern auch reaktive Materialien verarbeiten, wie Titan oder Titanlegierungen, oder auch Legierungen auf Nickelbasis. Diese Werkstoffgruppen sind im Flugzeugbau wichtig. Inzwischen bietet Concept Laser auch eine X line 2000R mit Multilasertechnik an. Dies könnte hinsichtlich der gesteigerten Aufbaurate sowie eines nochmals größeren Bauraums (800 x 400 x 500 mm3) eine interessante Option für uns sein. Die neueste Technik hat für uns enorme Bedeutung: Wir investierten allein 2015 rund 2,5 Mio. EUR in Anlagentechnik und Werkzeuge, zudem rund 1 Mio. EUR in Forschung & Entwicklung.
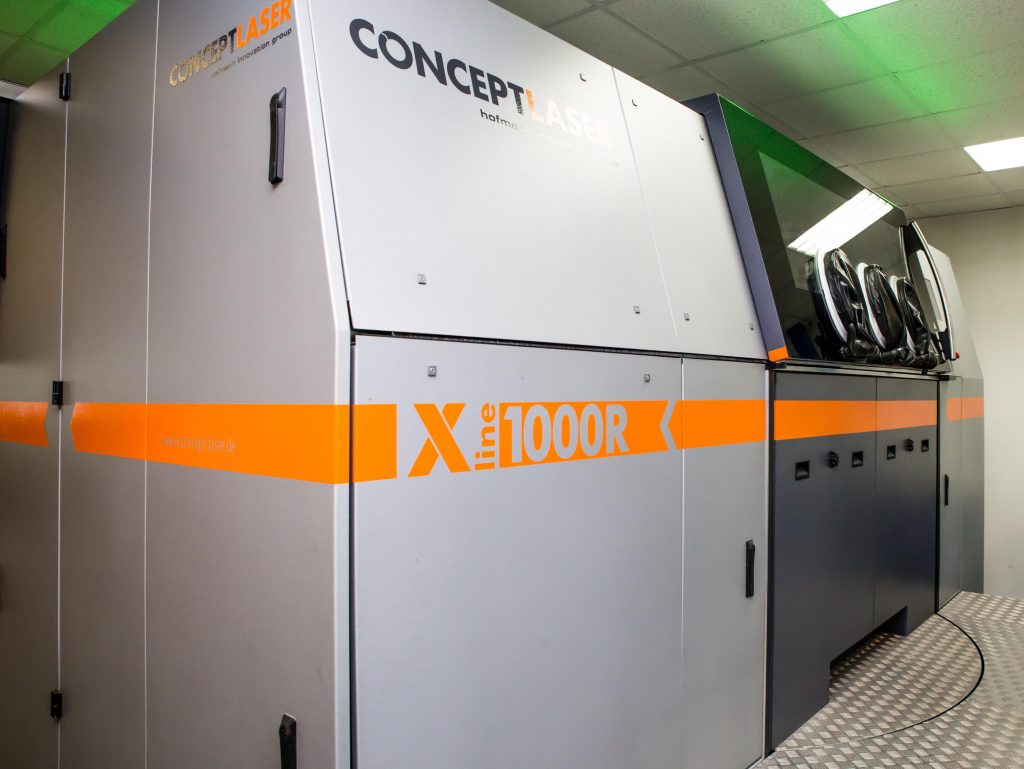
Welche neuen Erfahrungen konnten Sie im Projekt sammeln?
Stéphane Abed: Der 3D-Metalldruck erfordert zwingend ein verfahrensgerechtes Konstruieren, um die Vorteile eines digitalen Ansatzes voll auszuschöpfen. In Bezug auf die Geometriefreiheit sind die Vorteile gewaltig und mit nichts zu vergleichen, was es in konventionellen Fertigungstechnologien gibt. Digitale Teile sehen anders aus, leisten mehr, sind tendenziell leichter. In bestimmten Losgrößenbereichen, ich meine damit bei kleinen und mittleren Serien, sind sie wirtschaftlich oft die bessere Alternative. Aber die Grenzen verschieben sich von Jahr zu Jahr nach oben, und das eröffnet AM immer neue Horizonte. Natürlich sind Aufgaben für Thales Alenia Space besondere Herausforderungen an das ganze Team. Aber dies bietet auch den Vorzug, sehr viel Know-how in Konstruktion, Entwicklung und Prozessgestaltung aufzubauen. Das gilt natürlich auch für unsere anderen Kunden aus der Luft- und Raumfahrt. Ich sage immer: Die Luft- und Raumfahrt ist eine gute Schulung und Übung, um ganz vorne bei additiven Strategien mitzumischen.
Florence Montredon: Um eine solche Qualität für die anspruchsvollen Anwendungen in der Raumfahrt zu erzielen, braucht es natürlich auch eine starke Partnerschaft zwischen Endnutzer und Hersteller. Da muss man sich auf den Partner verlassen können. Voraussetzung war eine enge Zusammenarbeit und wechselseitige Interaktion von Thales Alenia Space und Poly-Shape auch, um die ambitionierten Zeitpläne einzuhalten. Teamwork und Kommunikation sind sehr wichtig.
Spielte Funktionsintegration im Projekt eine Rolle oder nicht? Wie sehen Sie dies zukünftig?
Stéphane Abed: Das 3D-Aluminiumteil ersetzte 9 Teile des früheren Designs. Das alte Design war eine Anordnung zweier Sandwich-Wabenplatten mit Metalleinsätzen und gefrästem Steg, die verschraubt und verklebt montiert wurden. Diesen Aufbau mit Montageaufwand konnten wir nun in einem Schuss in einem einzigen Bauteil abbilden.
Florence Montredon: Es ist klar, dass wir AM als guten Kandidaten für weitere Projekte identifiziert haben. Leichtbau, uneingeschränkte Geometriefreiheit, Funktionsintegration sowie Zeit- und Kostenvorteile sprechen eindeutig für diese Technologie. Auch der Arabsat 6B-Satellit, der im November 2015 in Französisch-Guyana in die Umlaufbahn gebracht wurde, hat 3D-Bauteile an Bord. Unsere Erfahrungen führen uns aber auch noch weiter. In Zukunft möchten wir auch thermische Kontroll- oder Radio-Funktionen direkt auf oder innerhalb der 3D-Strukturen integrieren. Also Funktionsintegration als nächste Aufgabe. Auch dies ist eine logische Konsequenz aus den Potenzialen von AM.
Was fällt Ihnen zum Stichwort Materialien ein?
Florence Montredon: Neue Materialien für AM sind natürlich ein Bereich von großem Interesse. Spezifische Legierungen aus Pulver werden wahrscheinlich zukünftig entwickelt und validiert werden, um mehr Anforderungen in den Bereichen Leichtbau, Funktionsintegration oder Beanspruchung gerecht zu werden. Für Weltraumanwendungen benötigen wir generell hohe Festigkeit, Steifigkeit und Korrosionsbeständigkeit der eingesetzten Materialien. Insbesondere für die Stabilitätsanforderungen von Wissenschafts- und Beobachtungssatelliten sollen die Materialien eine sehr geringe thermische Ausdehnung aufweisen.
Kommen wir bitte zu den Perspektiven des pulverbettbasierten Laserschmelzens von Metallen. Welche Trends sehen Sie mittel- und langfristig durch AM-Technologie auf die Luft- und Raumfahrt zukommen?
Florence Montredon: Ich glaube, dass der 3D-Metalldruck neue Produkte ermöglicht, auf Basis eines sehr integrierten Ansatzes von Funktionen. Die Größe der Teile und die Aufbaugeschwindigkeiten werden sich wohl auch erhöhen. Das ist natürlich eine echte Herausforderung für die Maschinen- und Anlagenbauer. Ich glaube auch, dass zukünftig Technologien stärker kombiniert werden müssen, um den maximalen Nutzen für das Endprodukt auszunutzen. Das ist ein Gedanke für hybride Teile oder das hybride Bearbeiten, also AM und Fräsen, AM und Fügetechnik oder die Montage von AM-Teilen und laserbearbeiteten Profilen. In allen denkbaren Fällen spielt Lasertechnologie eine wichtige Rolle. Die neuen Möglichkeiten werden die Fertigung der Zukunft prägen. Konventionelle Technologien werden durch neue Technologien ergänzt werden. Sie wachsen zusammen, werden teilweise, wie in unserem Fall, substituiert. Die Zukunft ist bunt und bietet vielfältige Antworten. Die digitale Prozesskette des 3D-Druckens wird dabei Impulse setzen. Für neue Produkte mit Eigenschaften, die die heutigen Lösungen übertreffen und für neue Fertigungskonzepte, die Gewicht, Zeit und Kosten sparen.
Was erwarten Sie auf Sicht von den Maschinen- und Anlagenbauern?
Stéphane Abed: Eine junge Technologie wie das Laserschmelzen bietet hohe Chancen, aber auch Risiken. Das gilt für die Anlagenbauer und uns Anwender genauso. Technischer Fortschritt im rasanten Tempo erzwingt ständiges Investieren in die neueste Technik, um die Wertschöpfung zu verbessern. Beim 3D-Drucken liegen die Innovationsschübe auf einem Niveau vergleichbar der Computerindustrie. Als täglicher und inzwischen langjähriger Anwender der Technologie wird Poly-Shape zukünftig mehr Qualitätsmanagement und eine höhere Produktivität im Fertigungsprozess benötigen. Die Teile, die wir produzieren, sind funktionell höchst anspruchsvolle, hohen Belastungen ausgesetzte und manchmal sehr sensible Teile. Dies erfordert ein extrem hohes Qualitätsniveau, um die ambitionierten Anforderungen zu erfüllen. Das Qualitätsmanagement kann mit den neuesten Anlagen am Markt direkt im Herstellungsprozess durchgeführt werden. Concept Laser bietet dazu z. B. QM Meltpool 3D als Tool. Bislang übliche, zerstörende und teure Prüfungen entfallen dadurch. Der zweite Punkt betrifft die Aufbaugeschwindigkeit unter wirtschaftlichen Aspekten. Antworten dazu sind die Multilasertechnik und weitere Anstrengungen der Maschinen- und Anlagenbauer.
Wir danken für das Gespräch.